Recycled Crushed Aggregate
For more sustainable construction practices
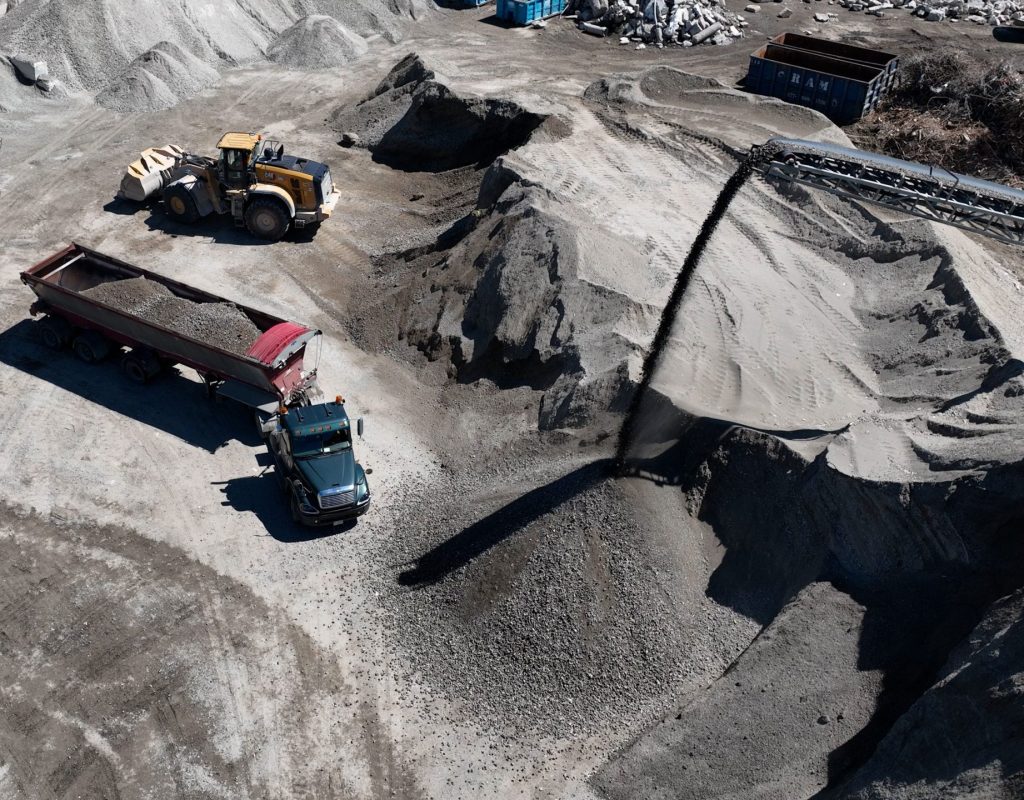
Asphalt and concrete are 100% recyclable and can be reused as valuable construction materials. Recycled Crushed Aggregate (RCA) is asphalt pavement and/or concrete reclaimed from old roads and structures.
The Ontario Provincial Standard Specifications (OPSS1010), jointly administered by the Ontario Ministry of Transportation and the Municipal Engineers Association, sets the standards for road construction and materials use in the province.
RCA is graded during processing and produced to specifications that provide equivalence to primary aggregates. RCA is subject to rigorous quality control and best practice processes and is a sustainable product that offers some of the greatest environmental benefits at a low cost.
Municipalities should consider sustainability as part of the initial project design of their linear infrastructure projects and:
✓ Include RCA use as part of their tenders.
✓ Mandate a minimum amount of RCA to be used.
✓ Harmonize and standardize municipal specifications through the OPSS1010.MUNI.
✓ Incentivize the use of RCA through provincial funding to municipalities.
✓ Prohibit municipalities from specifying “primary-only” in their tenders.
✓ Harmonize and standardize municipal specifications through the OPSS1010.MUNI.
✓ Mandate minimum 20% RCA of the aggregates used at the municipal, regional, and provincial levels.
180 million tonnes of aggregates are used annually in Ontario,
with more than 50% used in the construction of roadways, bridges, and tunnel infrastructure.
Only 7% or less currently come from recycled sources,
with much attributed to the Ontario Ministry of Transportation.
20% recycling rate by municipalities could avoid extracting up to 33 million tonnes of new aggregate per year in Ontario.
That would result in annual cost savings of $264 million and GHG emission reduction equivalent to taking 15 million cars off the road for a year!
BENEFITS OF RCA
Available
Readily available from construction and demolition activities at closer proximity to new construction projects. If not recycled, this precious resource will end up in landfills.
Economic
Lower direct project costs and wear and tear on roads from heavy truck transport, while building more sustainable infrastructure.
Sustainable
Expands life of existing pits and quarries, while diverting a valuable resource out of landfills. It significantly lowers energy use and GHG emissions associated with long-distance truck hauling and traffic congestion.
GTHA Aggregate Deficit
Rubble from roads and structures is diverted from landfills and delivered to a near-by recycling plant via dump trucks. The trucks’ contents are visually inspected at the entrance for the presence of organics, wood, rebar, plastics, significant amount of asphalt and other deleterious materials, as outlined in the OPSS1010.
Upon approval, trucks proceed to an off-loading (dumping) location. The stockpiled rubble material is then placed into a two-stage crusher by a wheel loader. The crusher reduces the size of the rubble pieces to smaller sizes at stage one and to stage two crushing via a conveyor belt.
Rebar and other metallic objects are removed by a magnet during the crushing process. Any other deleterious materials are detected visually by recycle plant personnel and manually removed prior to final screening to comply with gradation requirements.
The crushed and screened material is stockpiled. A separate stockpile containing visually significant amounts of asphalt and asphaltic concrete rubble is kept at the site and the material is added to the crushing of concrete process in limited amounts to comply with the OPSS1010 and gradation requirements. Lab testing of material is periodically conducted to ensure compliance with the specifications.
TARBA’s Quality Control Plan provides a technically sound manual for producing, utilizing, and ensuring the quality of recycled aggregates and can be a useful resource for producers, contractors and project owners. Adherence to this plan assures quality control of product standards specified in OPSS1010.
RCA Examples in Ontario
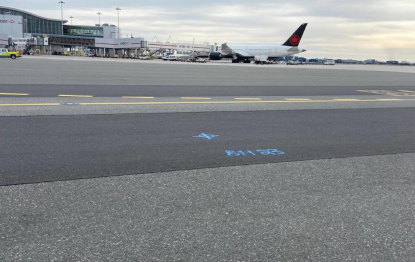
Toronto Pearson Airport Old Terminal 1
In 2006, Greater Toronto Airports Authority set an example of material reuse, recycling and remediation with the demolition of old Terminal One, Canada’s largest demolition contract up to that point.
The concrete rubble from the demolition of T1 structure amounted to 253,000 tonnes and an additional 10,000 tonnes of asphalt, all of which was processed and recycled on site, and then used as the apron’s sub-base holding up the final concrete and HMAC apron structure.
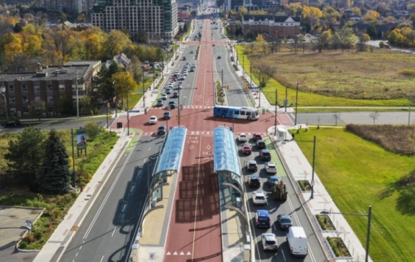
VivaNext in York Region
The VivaNext bus rapid transit (BRT) Yonge Street project in York Region utilized more than 250,000 tonnes of RCA, diverting more than 5,500 truck loads of concrete rubble from landfills. With the RCA source just 19 km away, and an efficient system in place where vehicles often backhauled material, this project exemplified sustainable and cost-effective material management. Watch the video here to learn more.
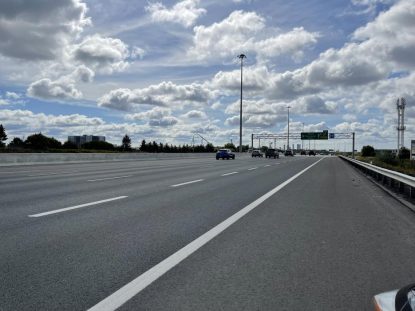
Hwy 400 Widening between Major Mackenzie Dr. & King Road
In 2017, the Ontario Ministry of Transportation used 300,000+ tonnes of RCA as unbound base and subbase, generating $1.2 million in cost savings for taxpayers. The RCA source was less than 10km to the project, significantly reducing the overall carbon footprint and especially greenhouse gas emissions.
The Ontario Ministry of Transportation, an early adopter and leader since the 1970s, uses more than 10 million tonnes per year of RCA in the construction and maintenance of the 400-series highways .
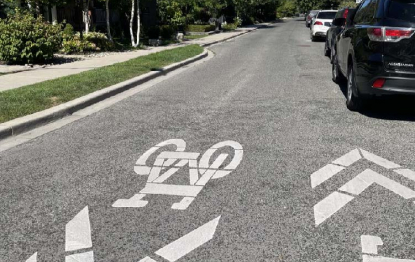
City of Toronto Greenwood Racetrack
The very first use of RCA as road base material in Toronto’s history was in 2002, showing no structural deficiencies more than 20 years later.
The east half of the former Greenwood Racetrack in Toronto saw the construction of 900 units and five streets, including underground sewers, watermain and other services.
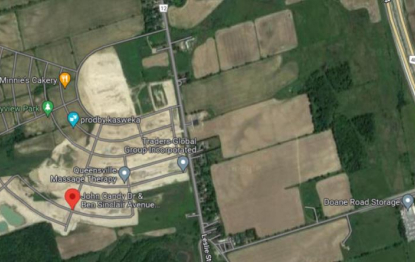
Town of East Gwillimbury
Although a smaller municipality than it’s GTA neighbours, in 2021, the town led the way by using 88% RCA in the construction of its Queensville Subdivision Phase 6, generating savings of $152,145 ($11.5/t).
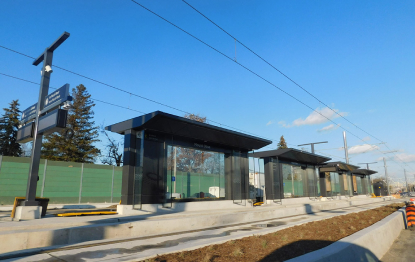
Finch LRT
Beginning in 2019, the construction of Light Rail Transit on Finch Avenue between Humber College Rd to Keele Street used 85,000 tonnes of RCM with no asphalt particles to replace Gran A, generating savings of $510,000 (saving $6.0/t).
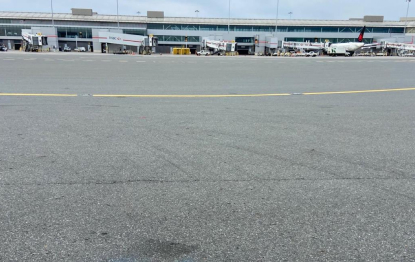
Toronto Pearson Airport Runway
Rehabilitation of Runway 06L/24R, Pearson’s second-busiest runway began in 2022. An estimated 25,000 tonnes of concrete were diverted from landfills and reused. Concrete from the runway pavement removal was used as the sub-base and base materials and recycled milling asphalt materials on approach roads in the vicinity of the runway.
The GHG emissions savings for every 10,000 tonnes that is recycled instead of newly extracted are equal to:
Resources
Using Recycled Crushed Aggregates Technical Seminar: EXP Presentation
Using Recycle Crushed Aggregates Technical Seminar: MTO Presentation
Using Recycled Crushed Aggregates Technical Seminar: Supplier Presentation
Webinar: Using Recycled Crushed Aggregates: Case Study of York Region’s VivaNext Project
Webinar: Sustainability in Action: Using Recycled Crushed Aggregates in Linear Infrastructure
RCA In the News
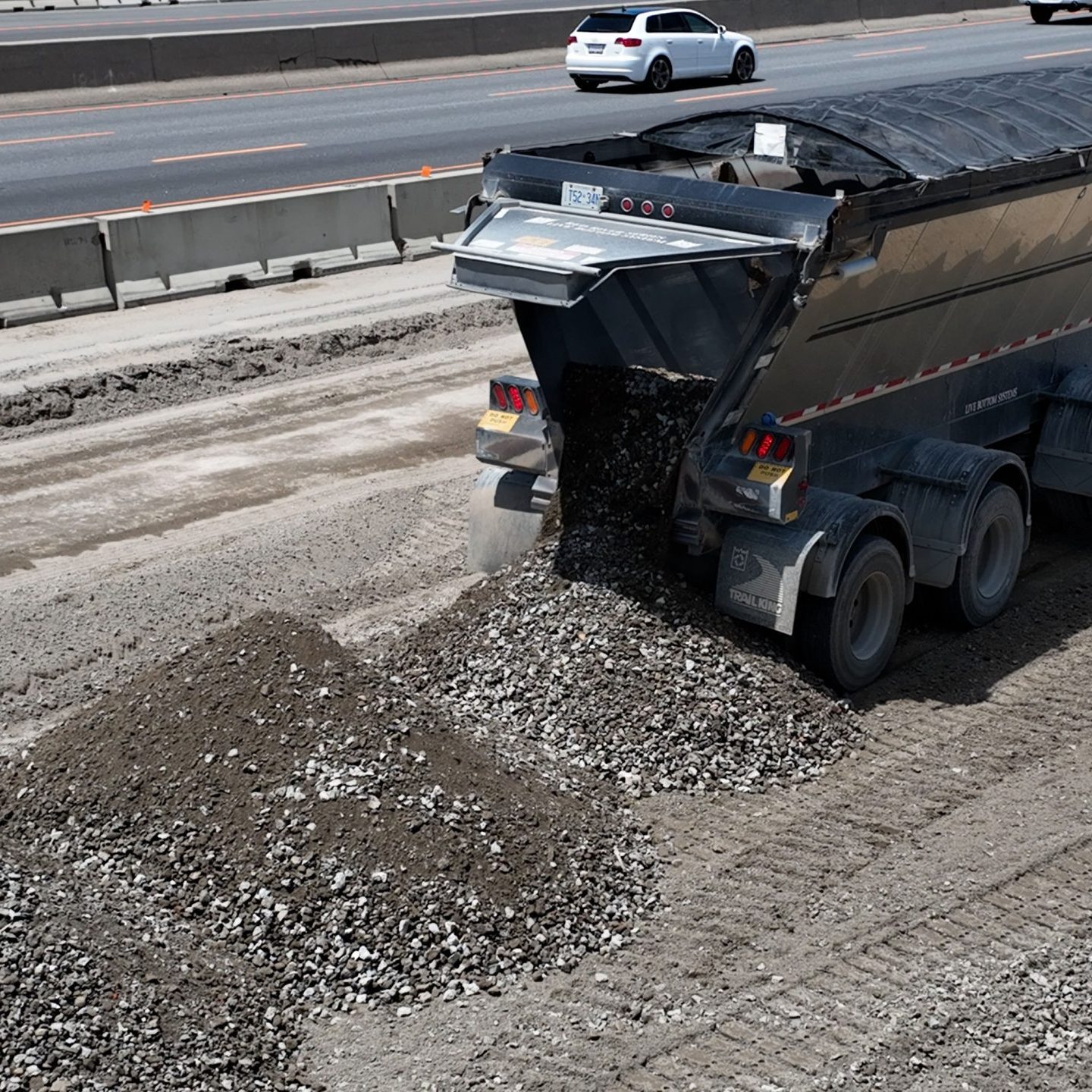
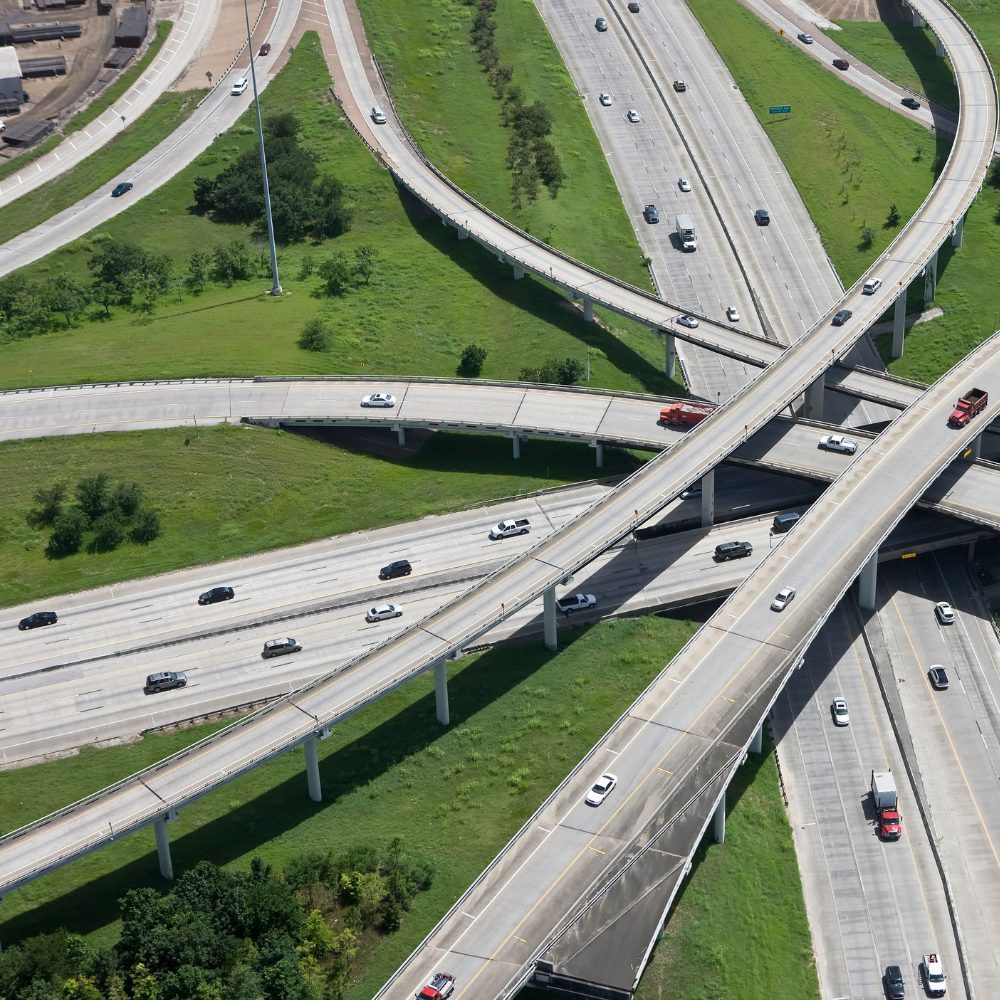
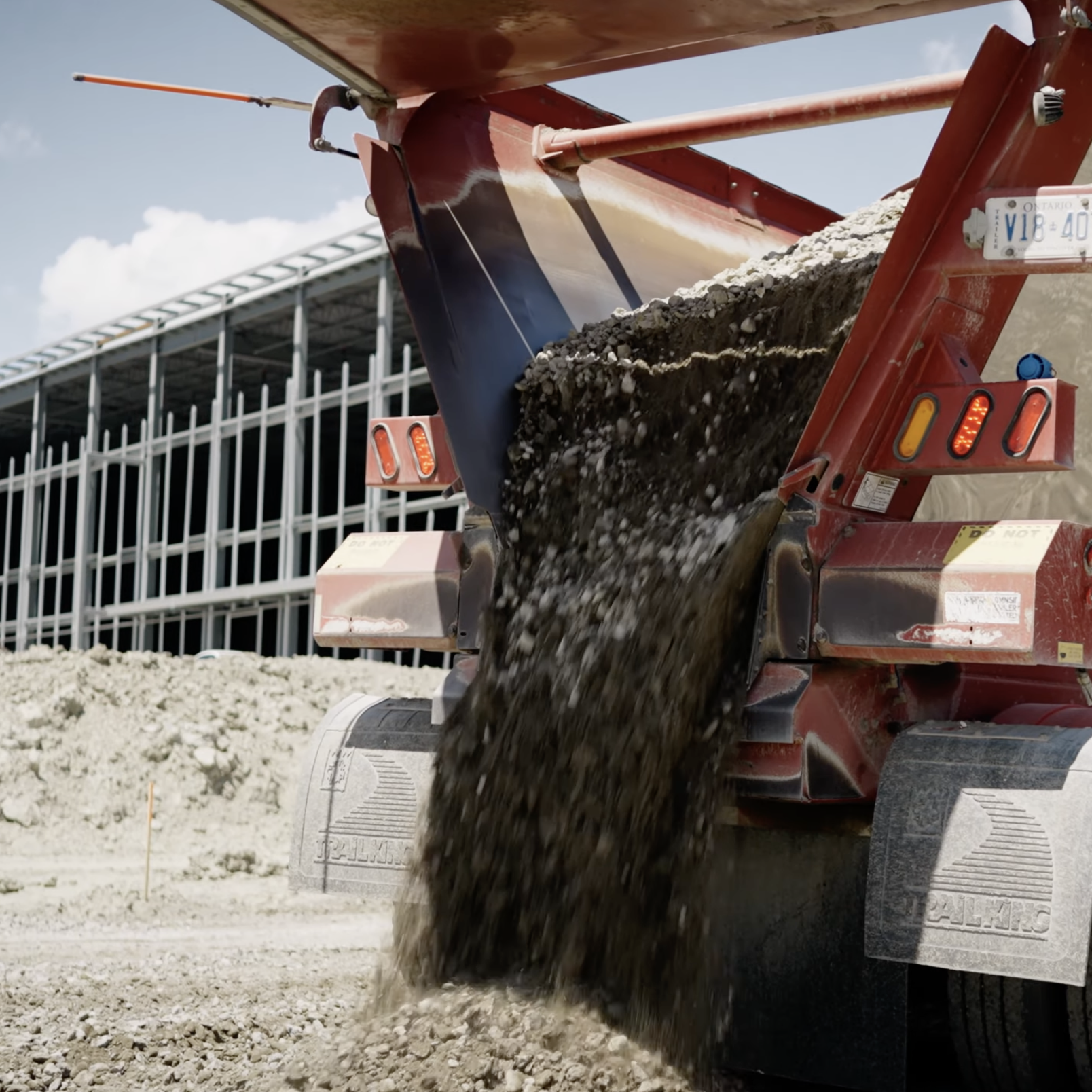
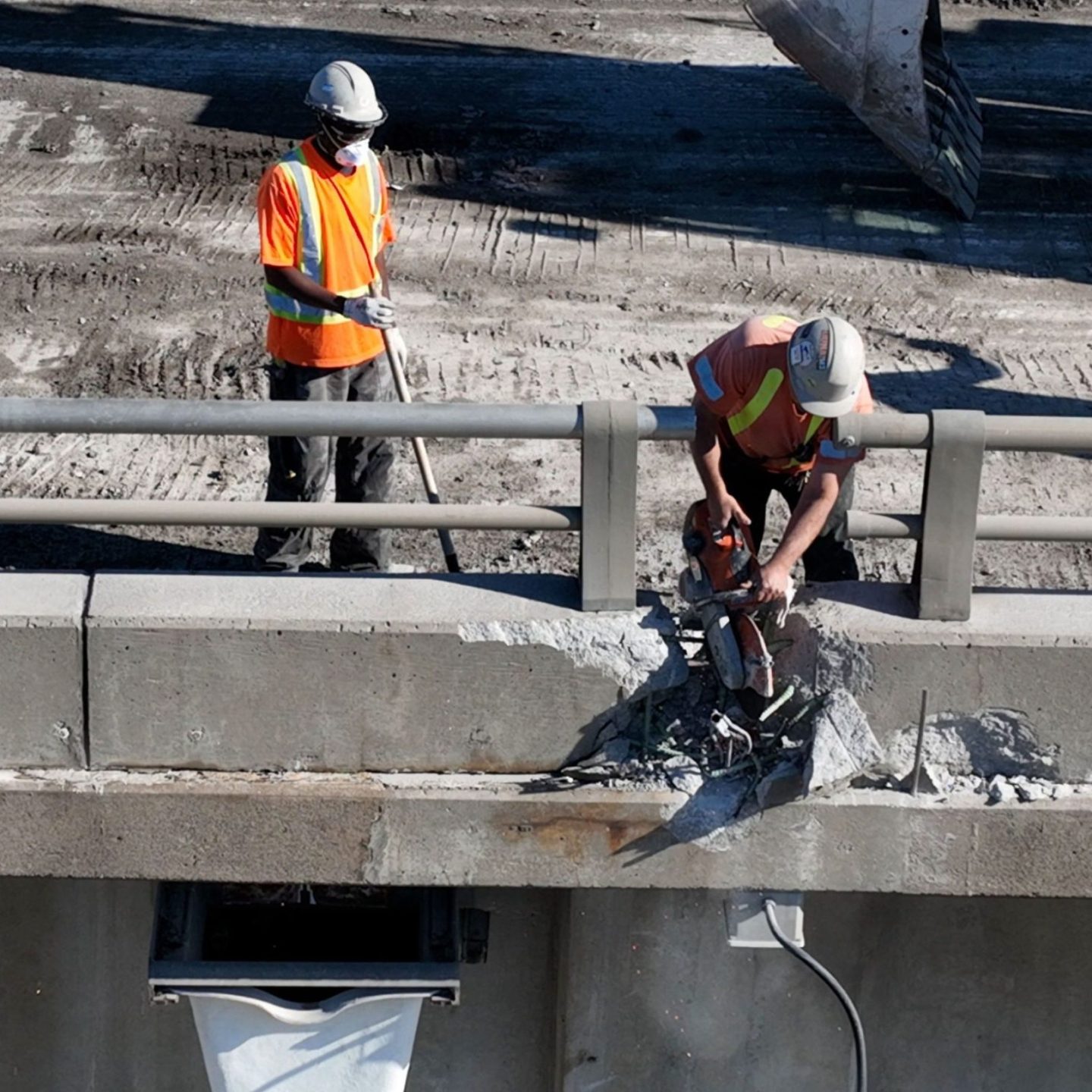
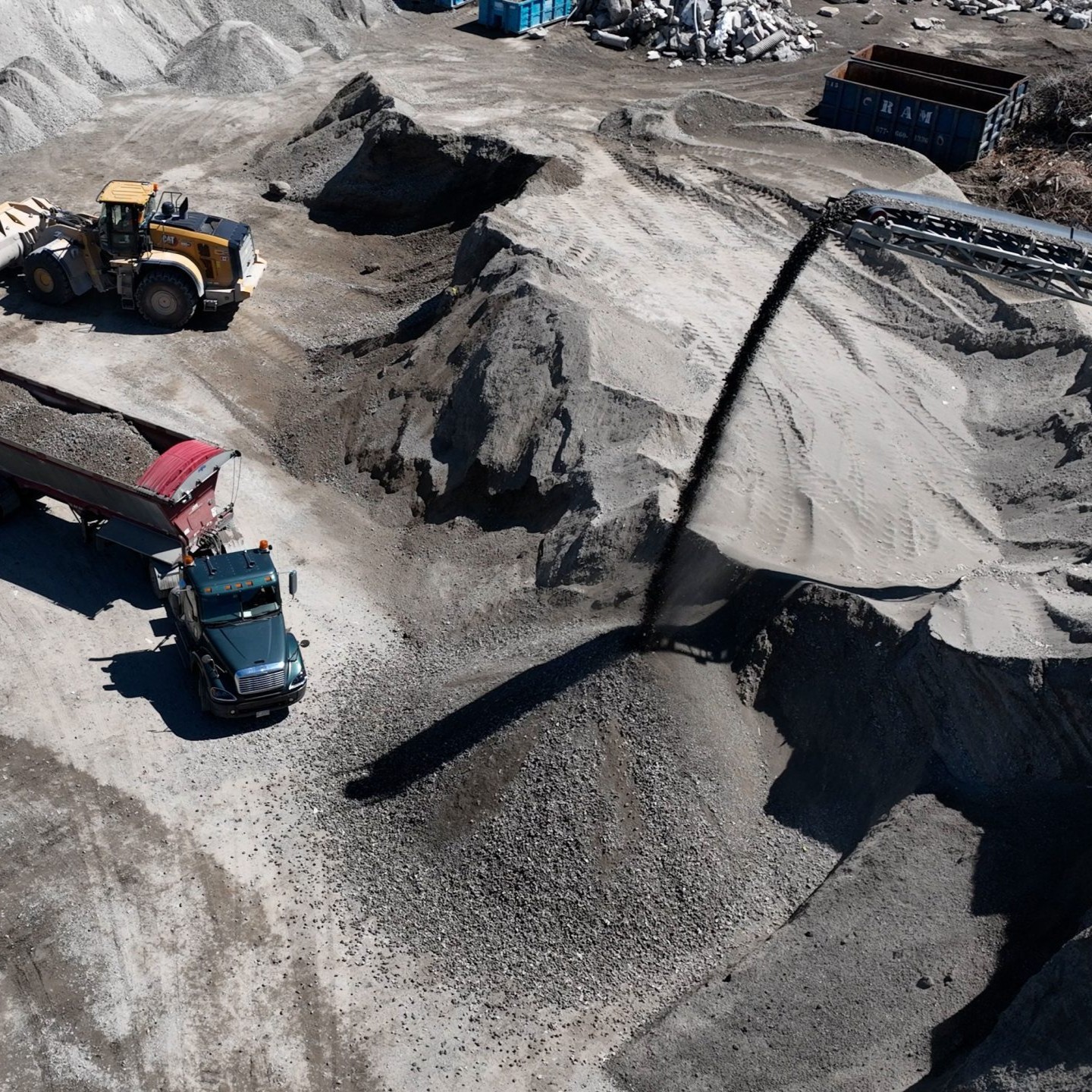
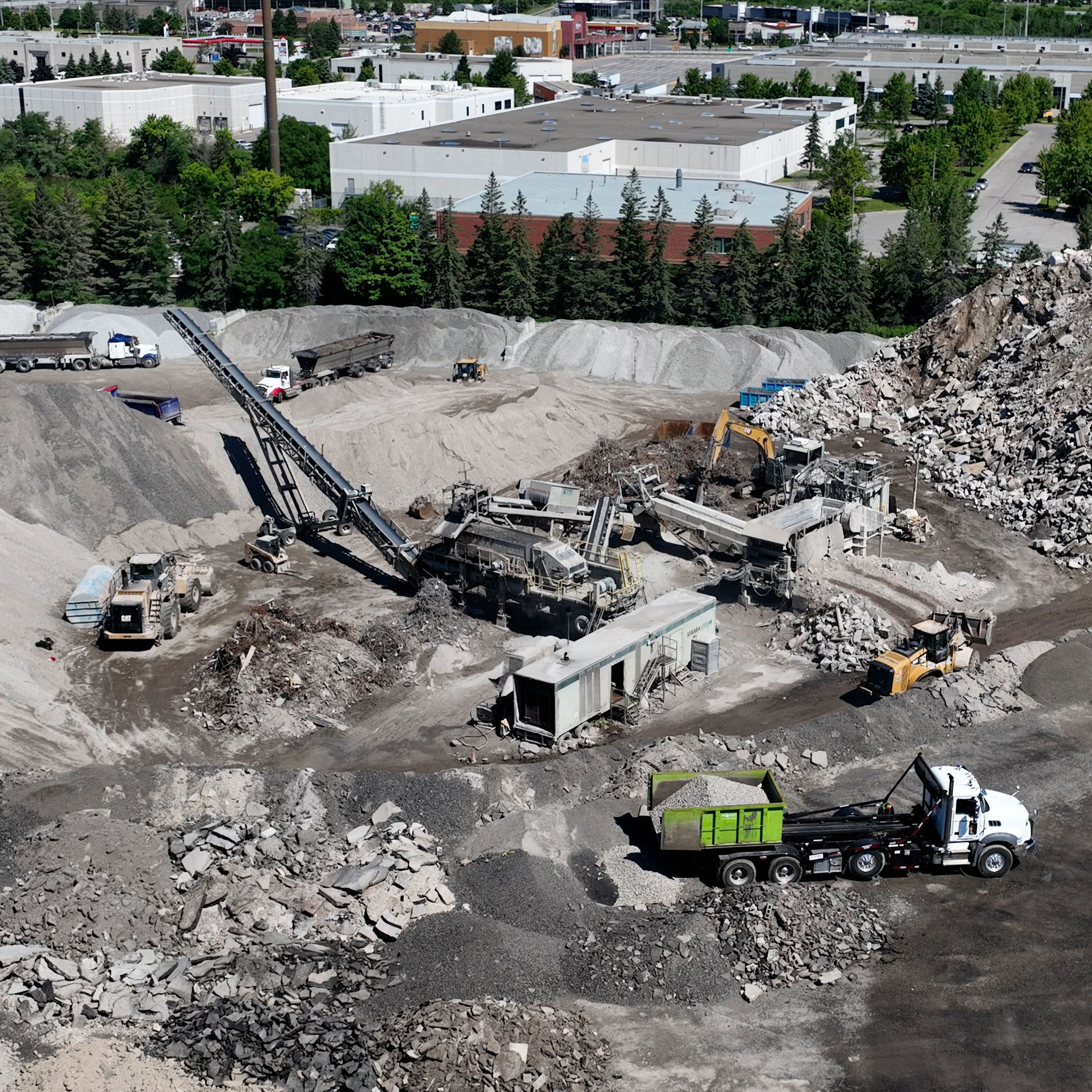
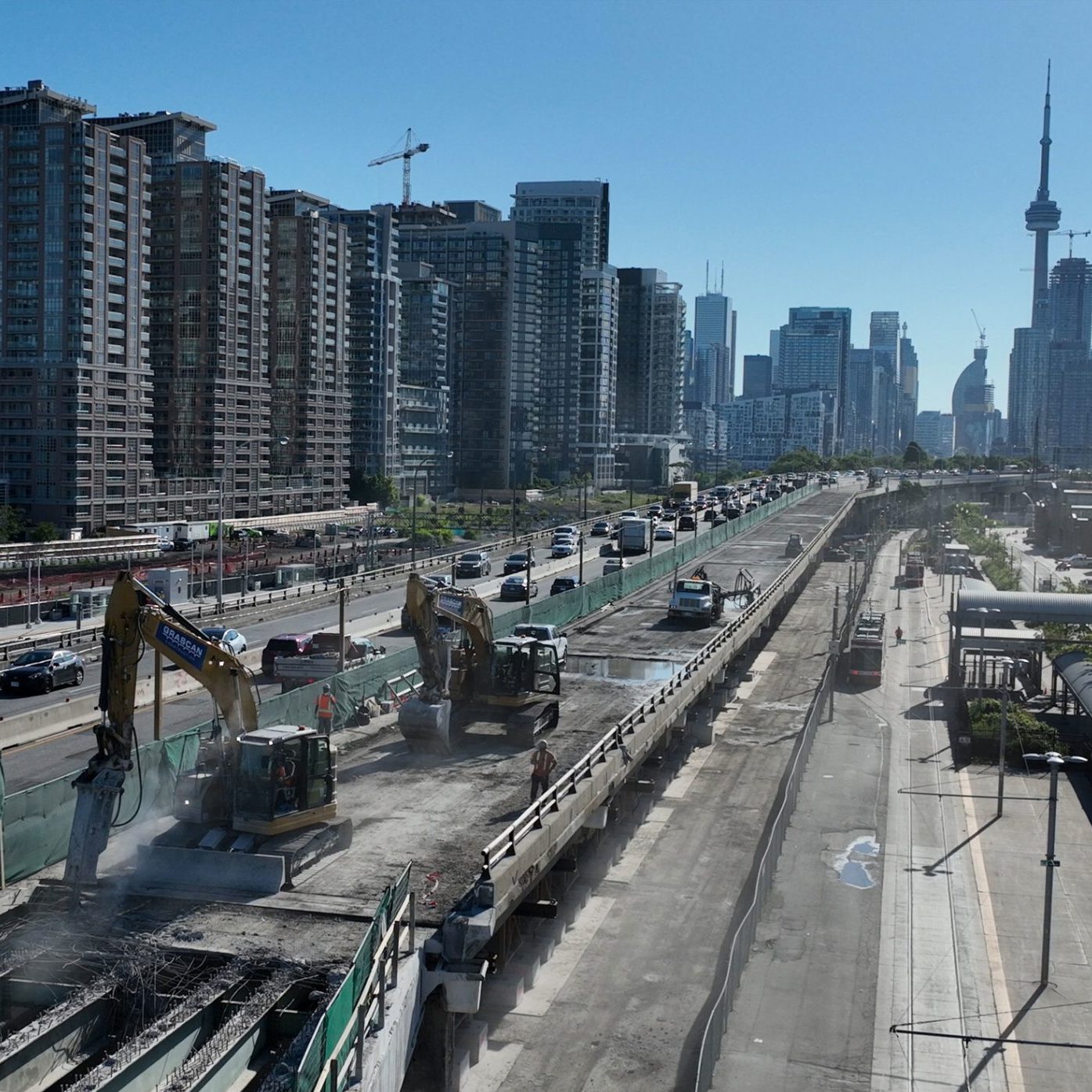
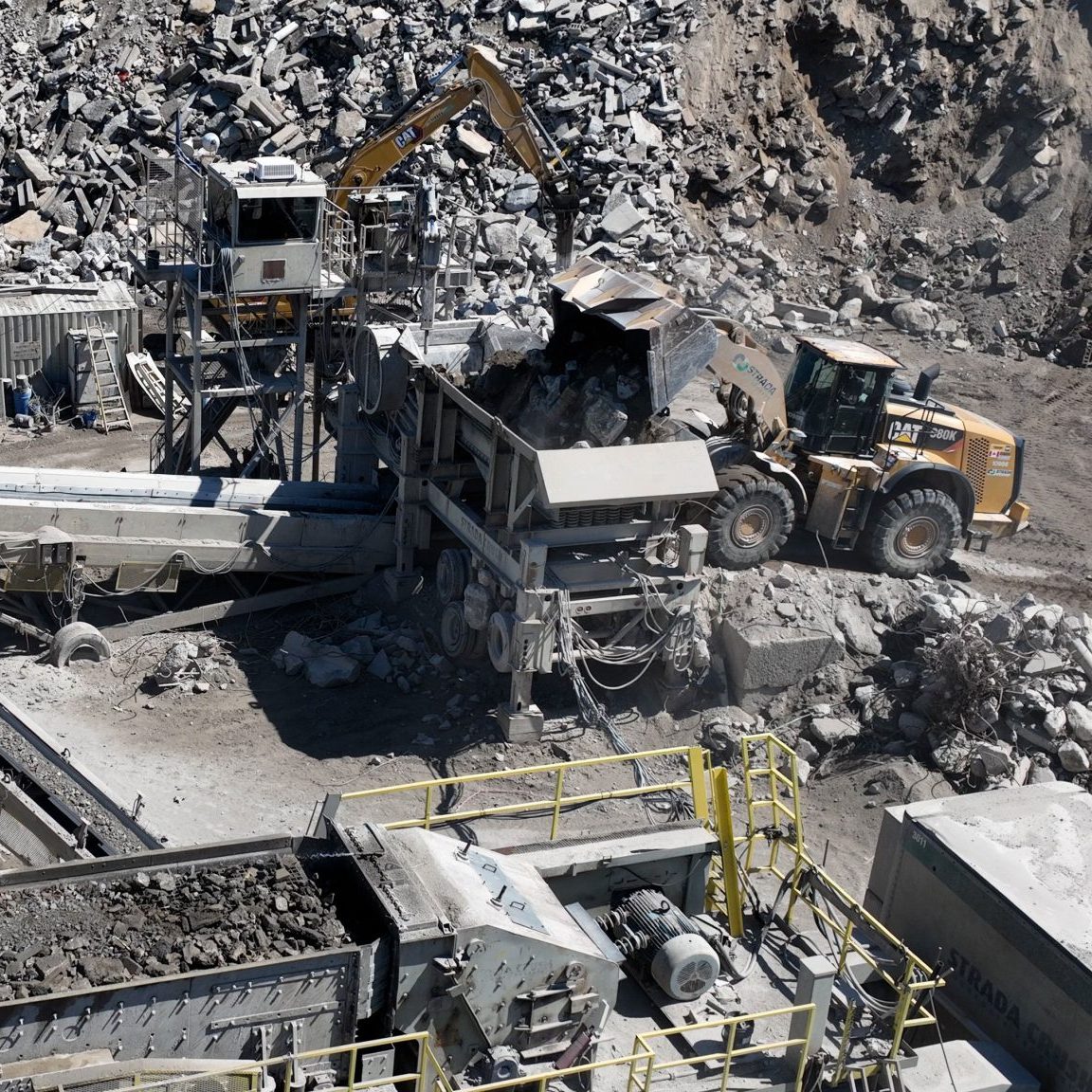
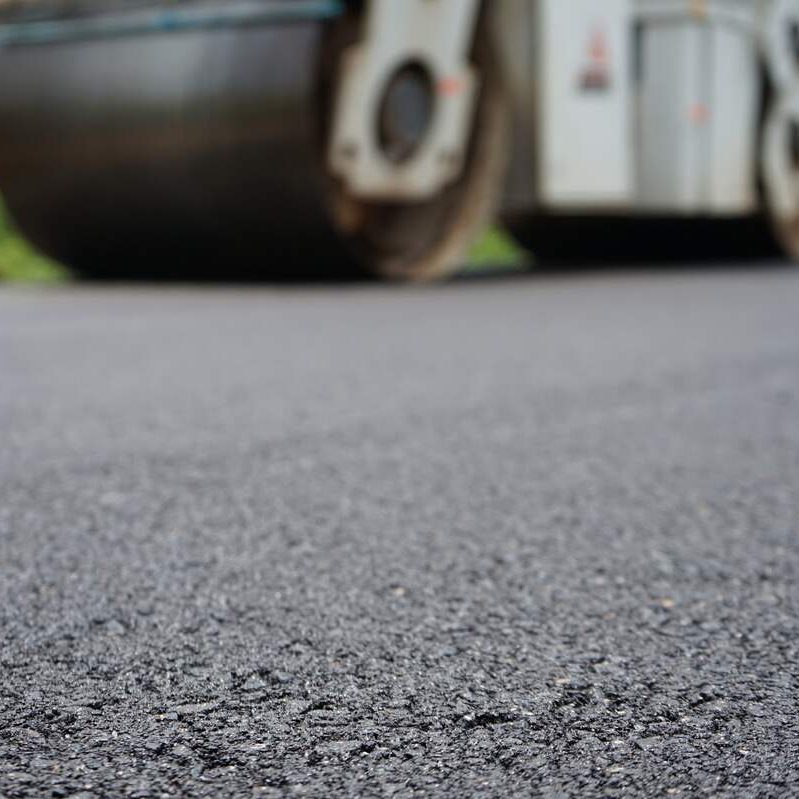
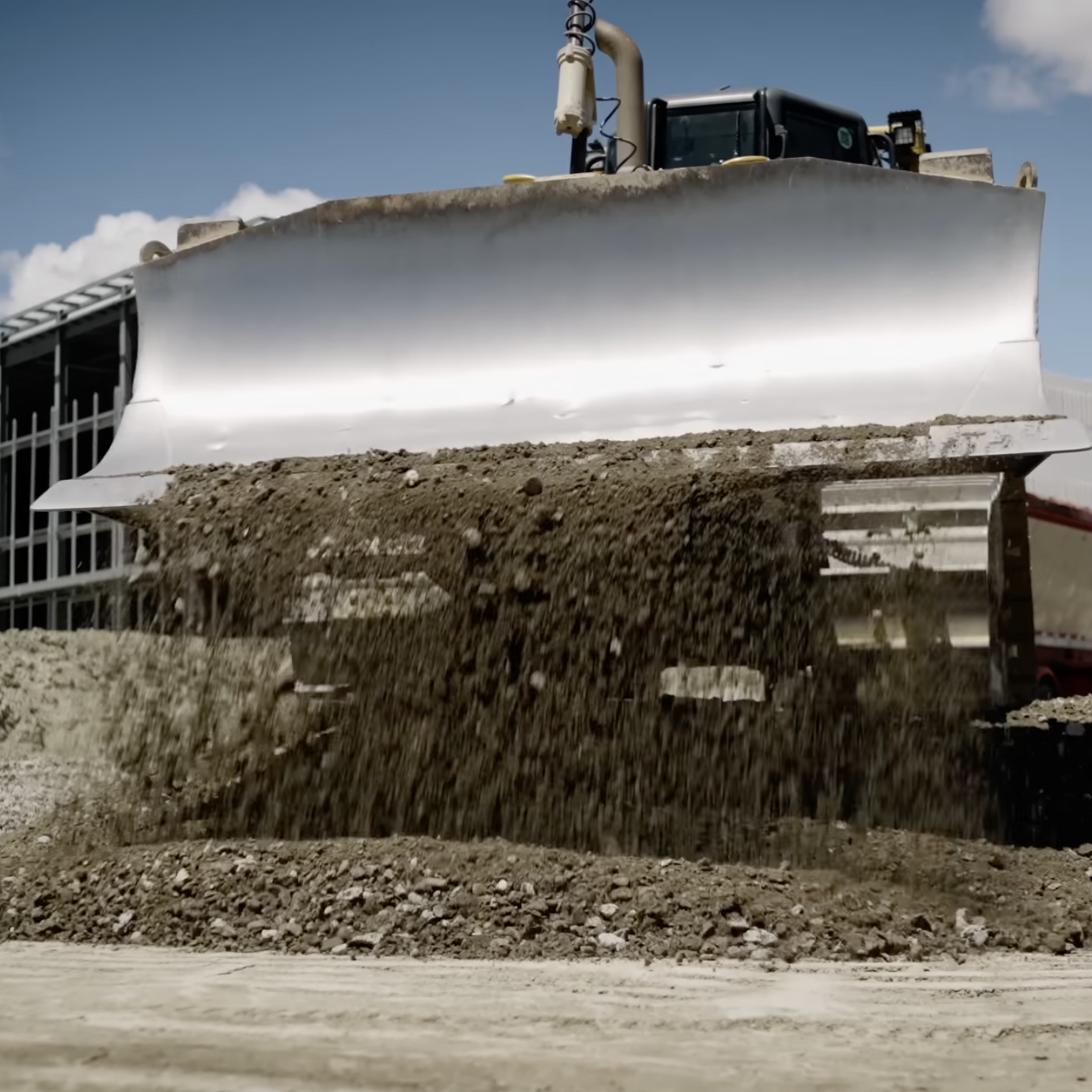
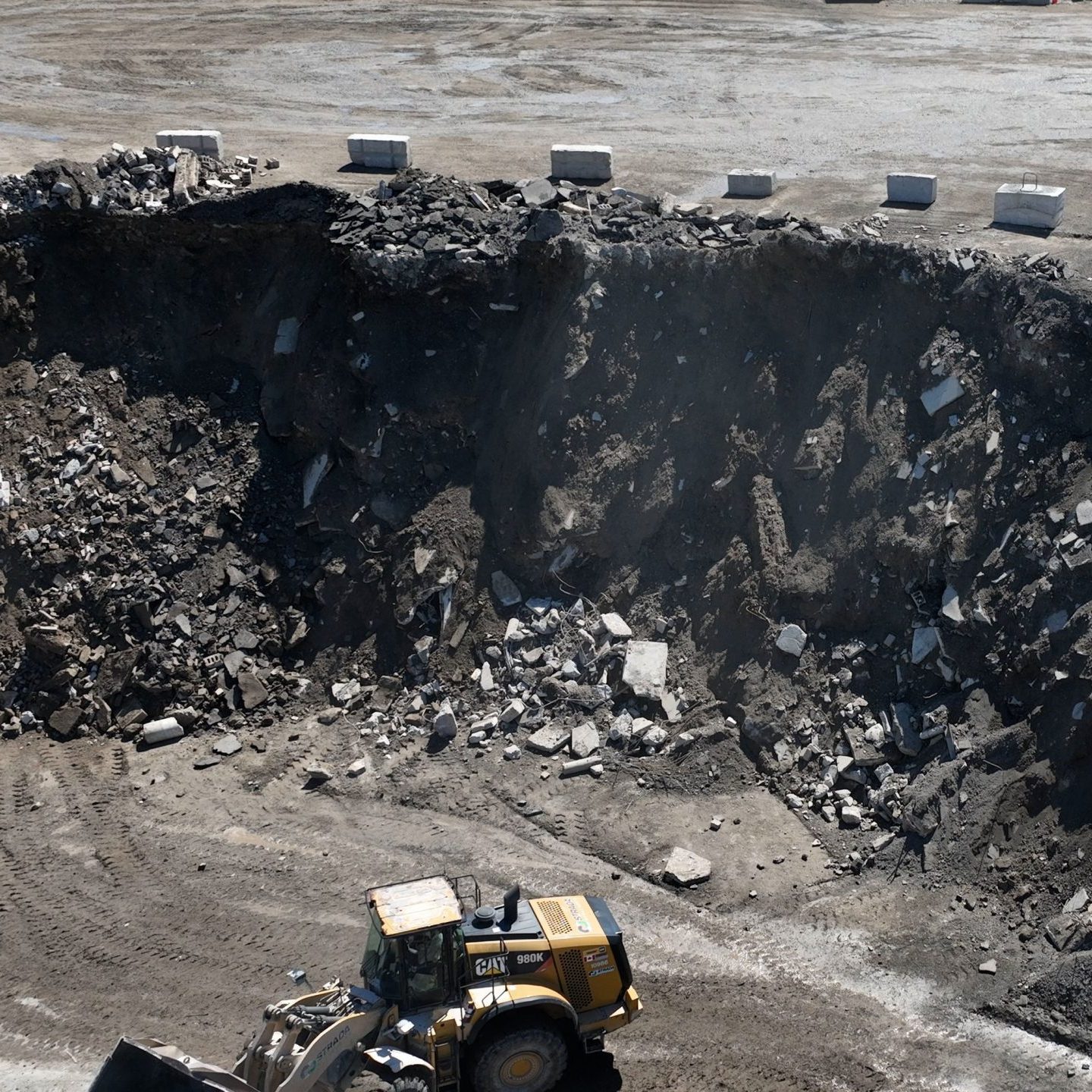
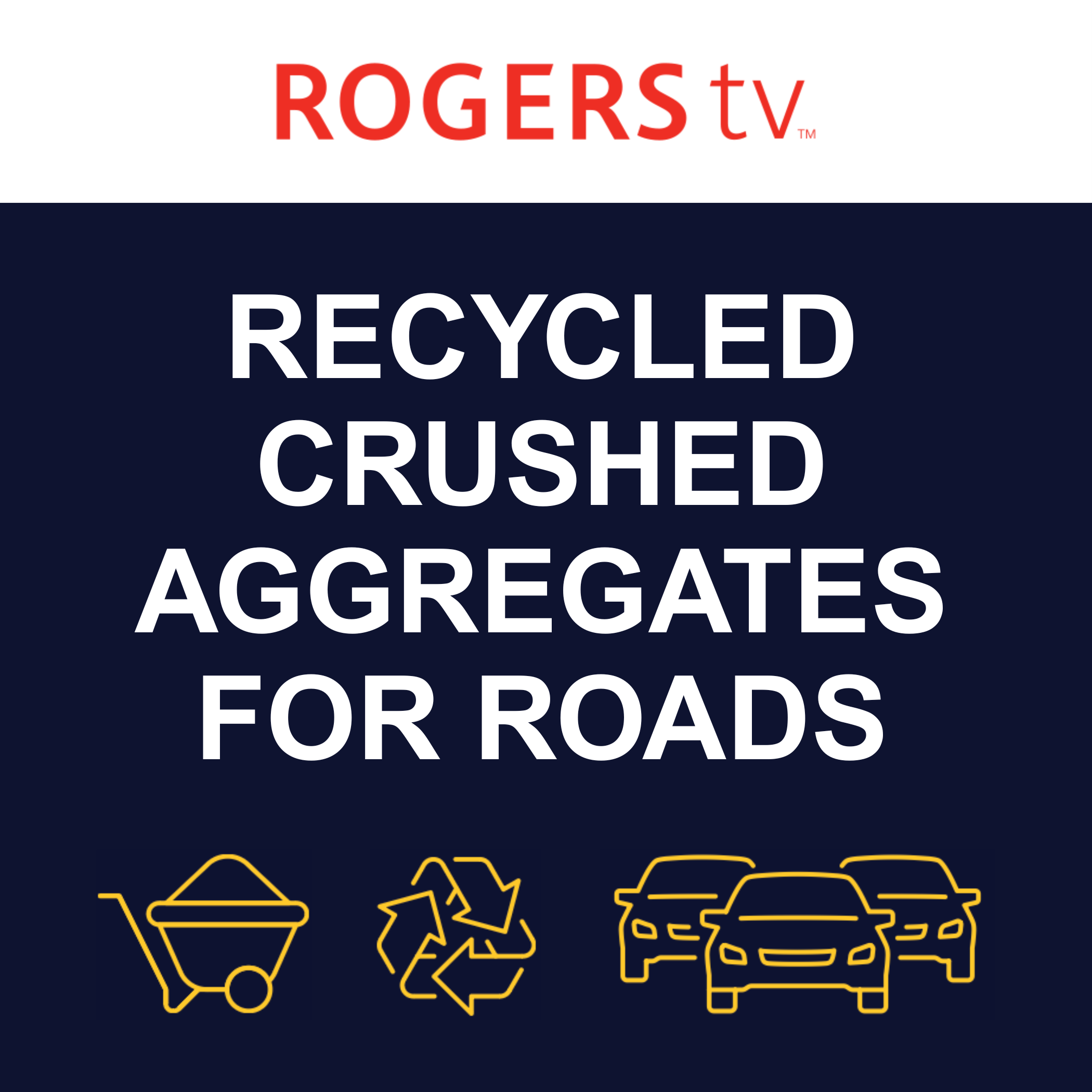
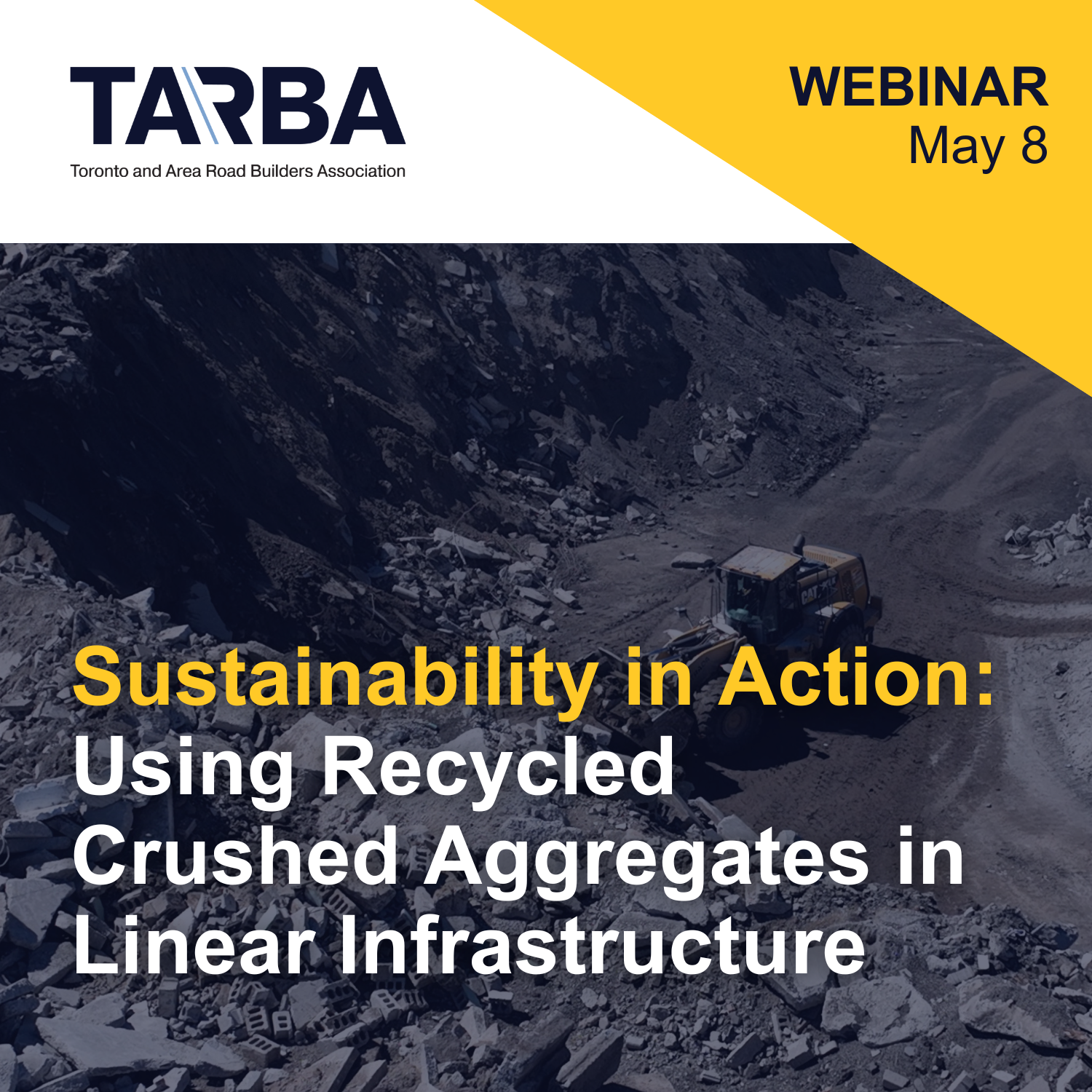
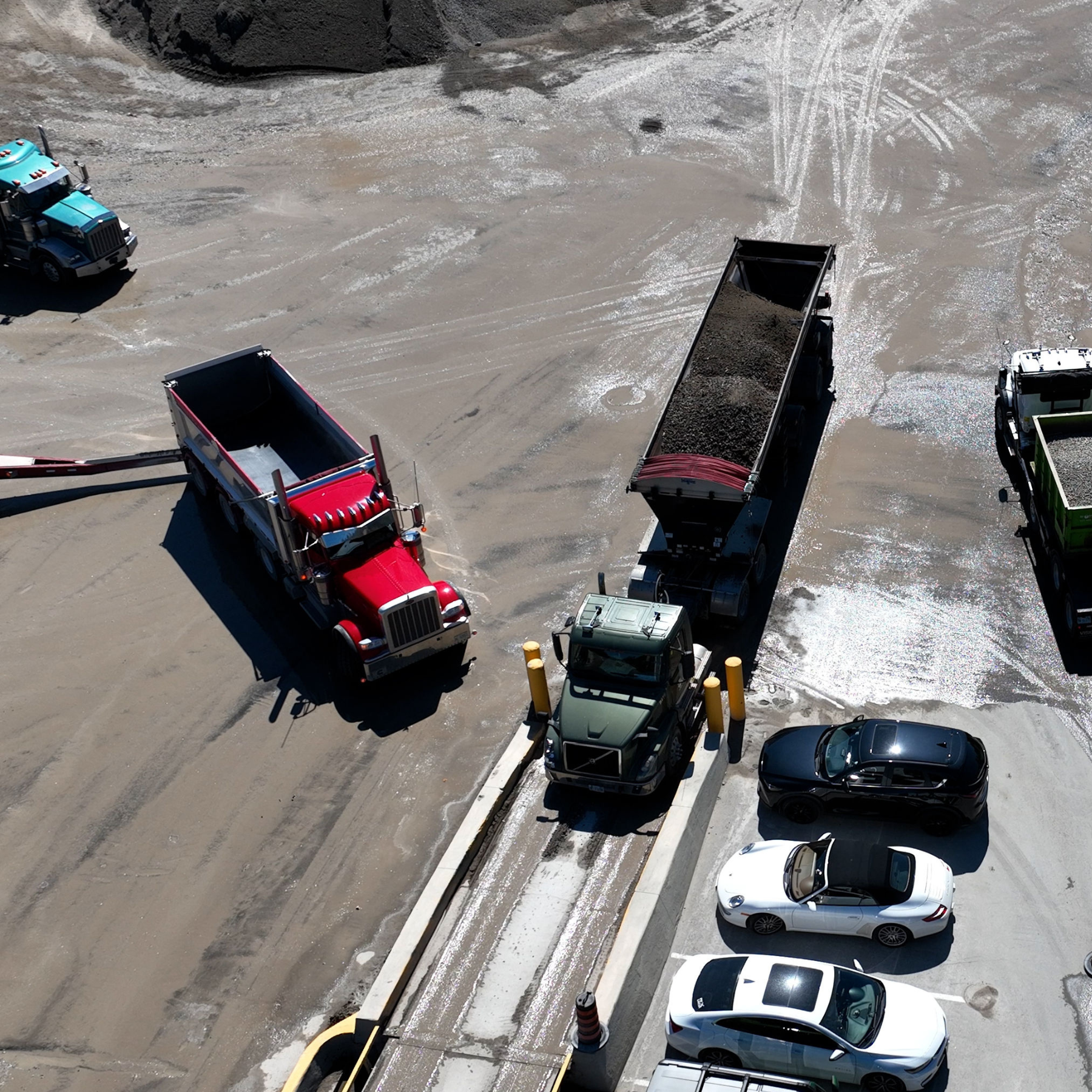
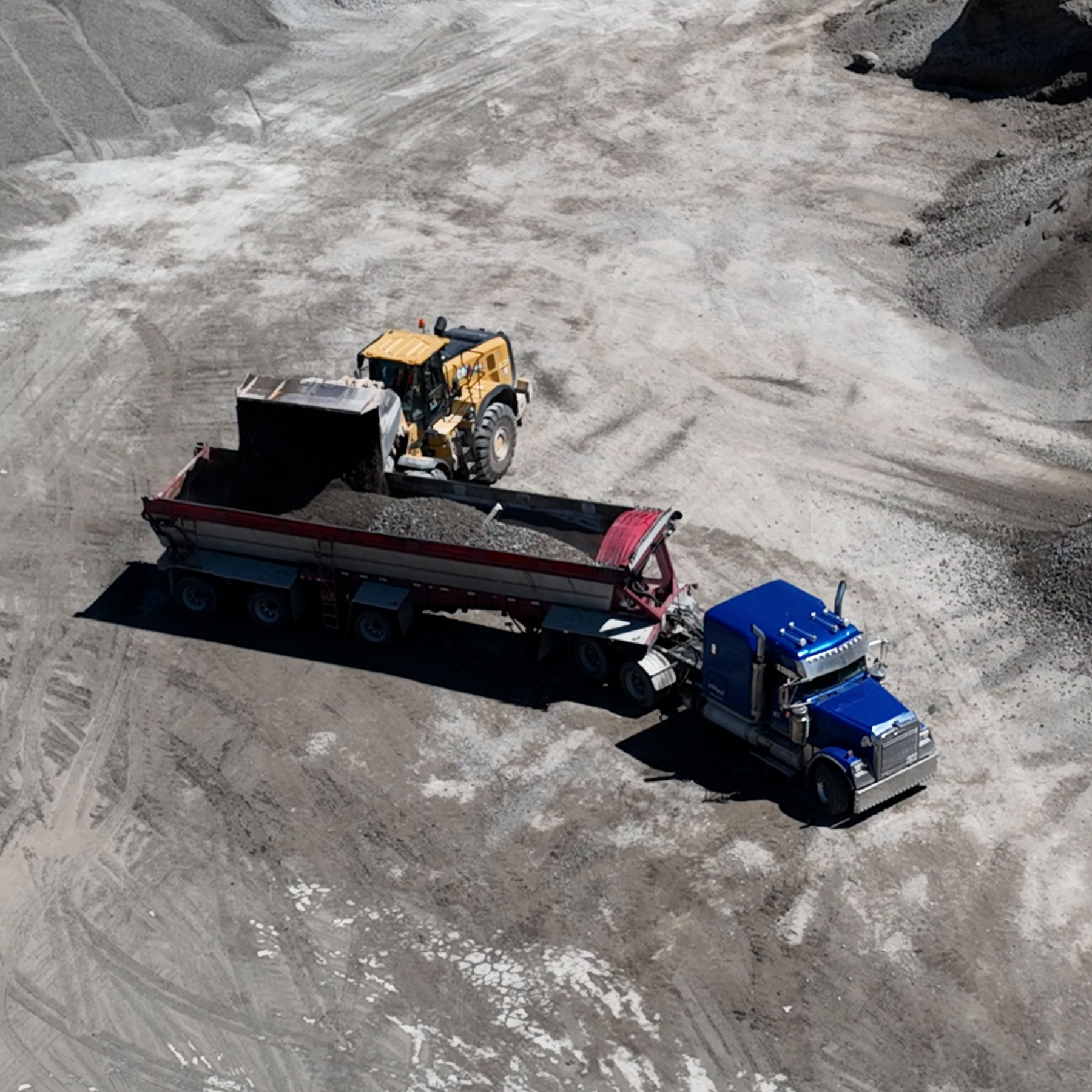
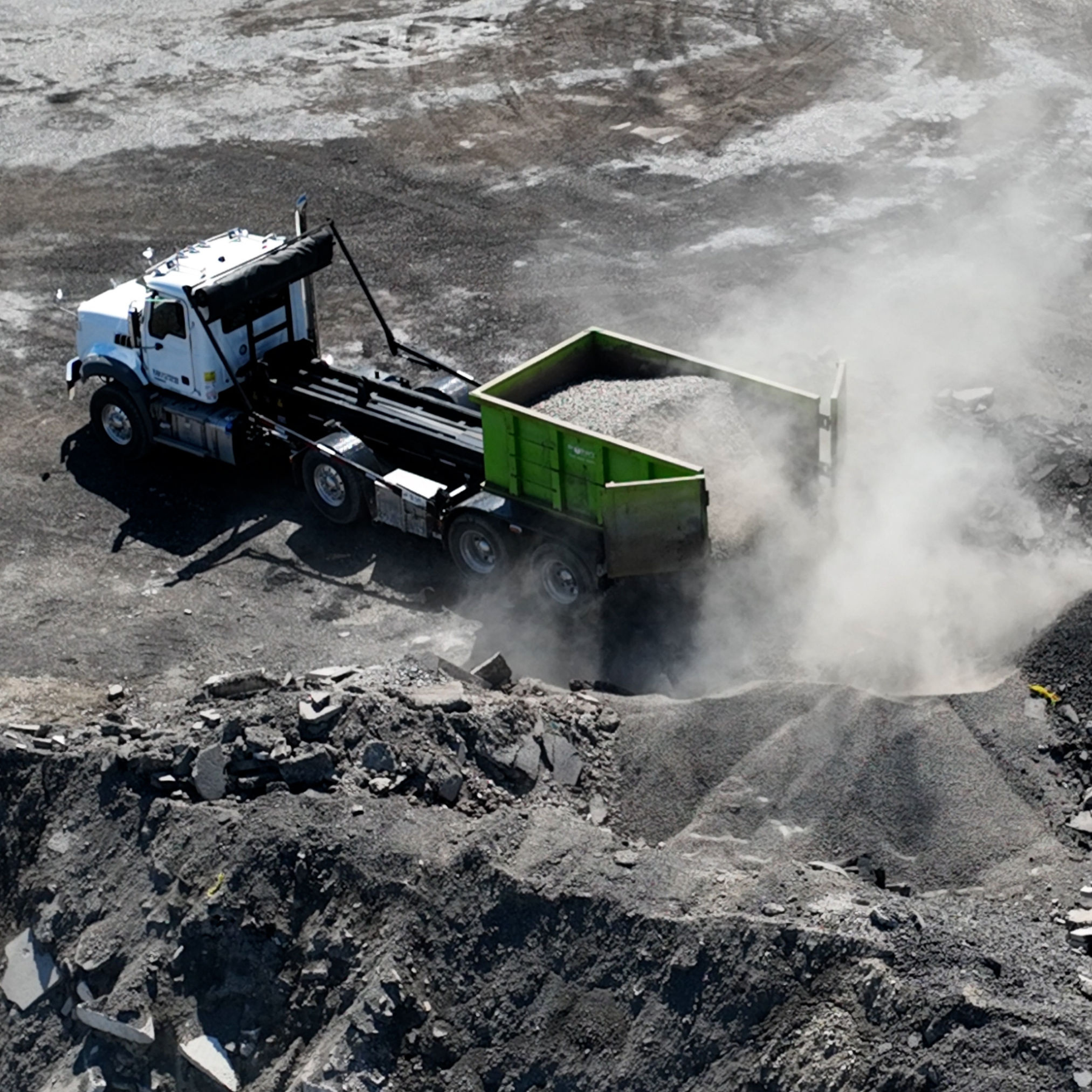
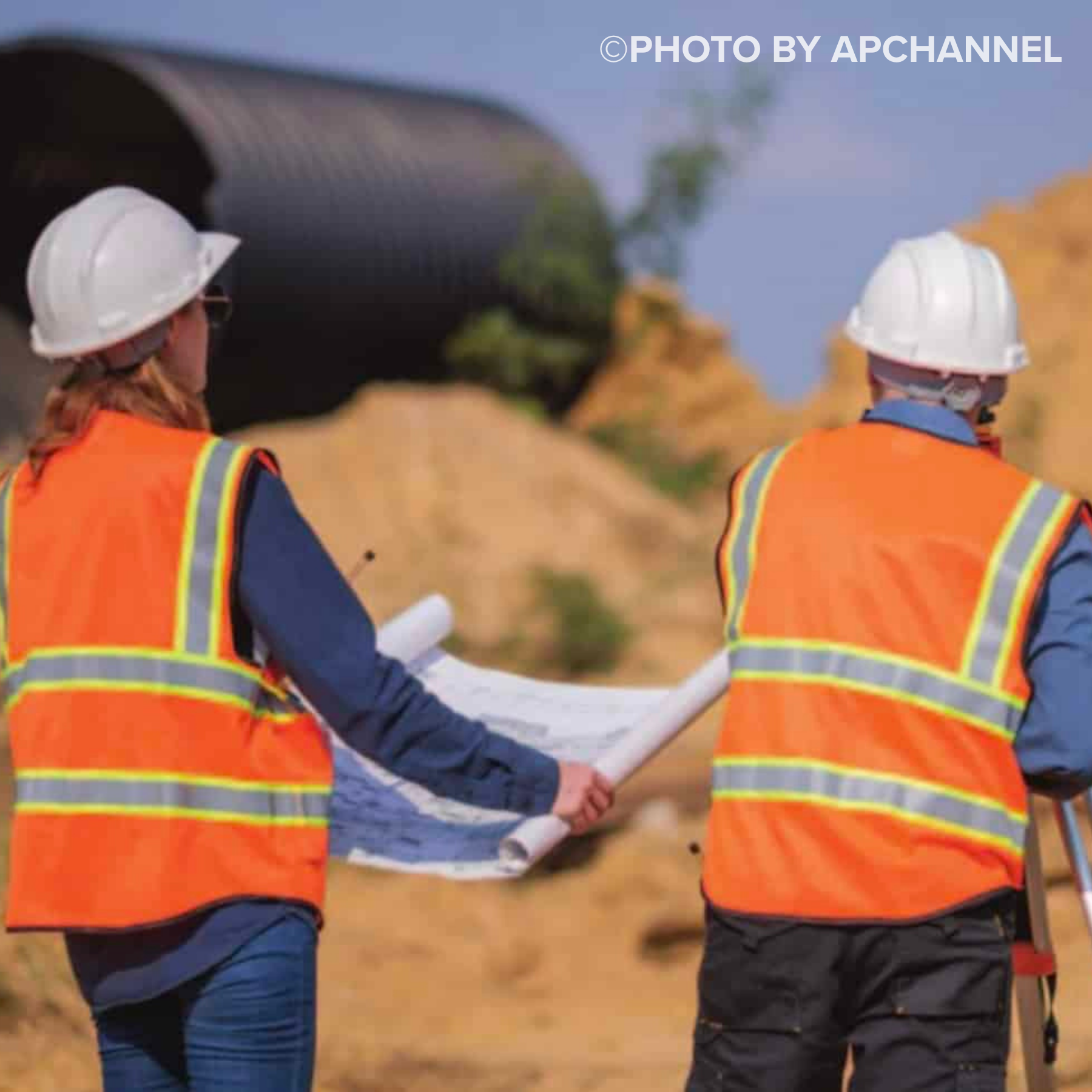
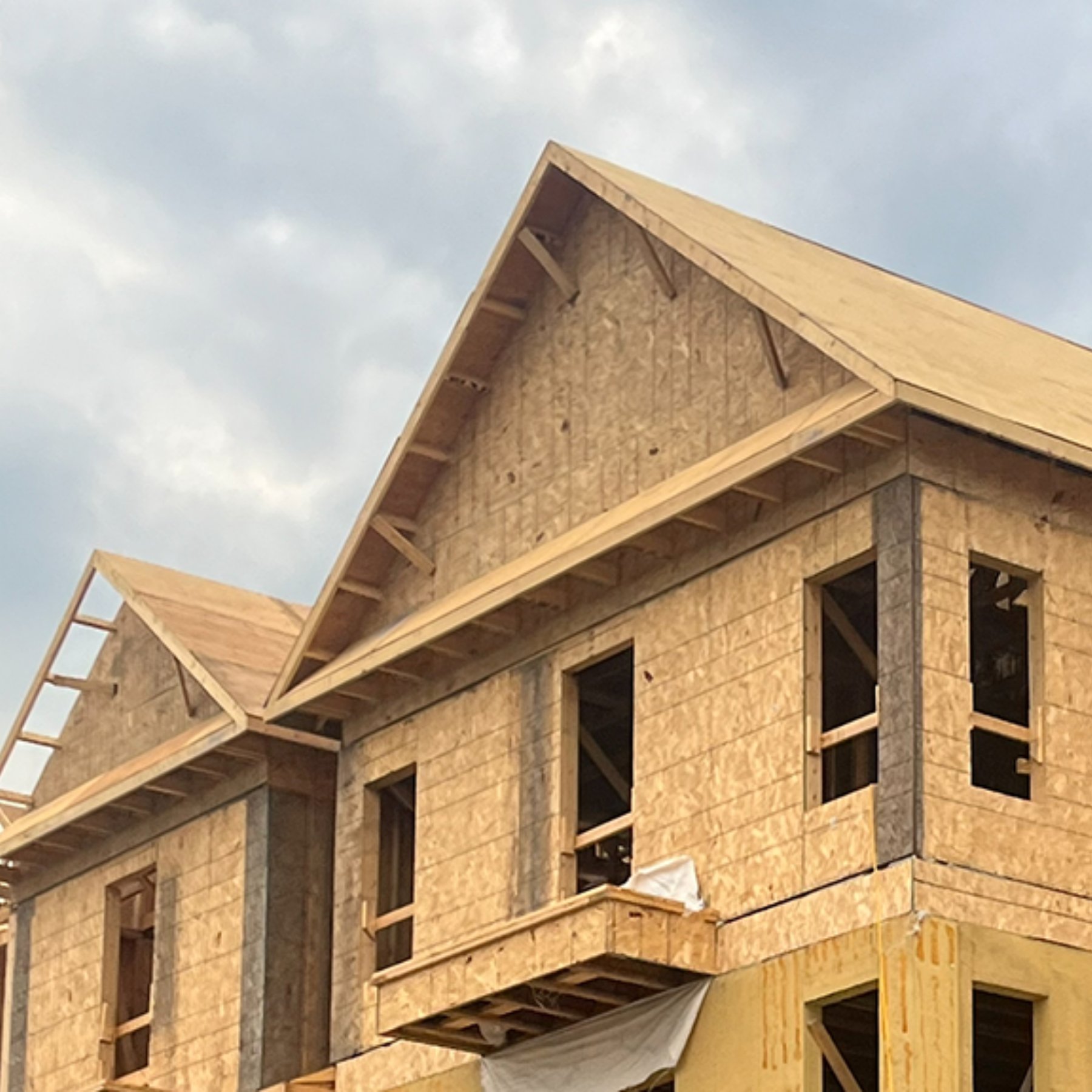
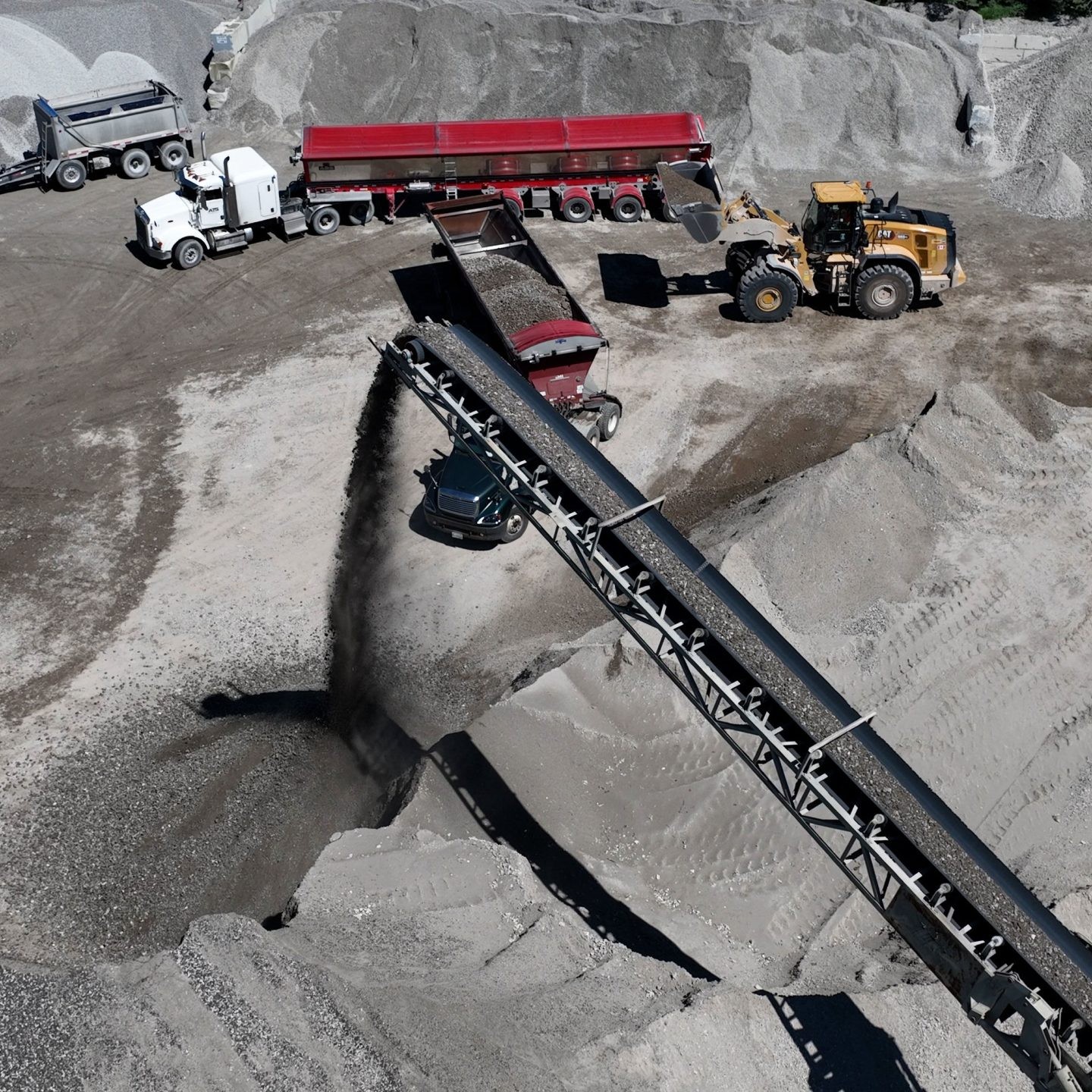
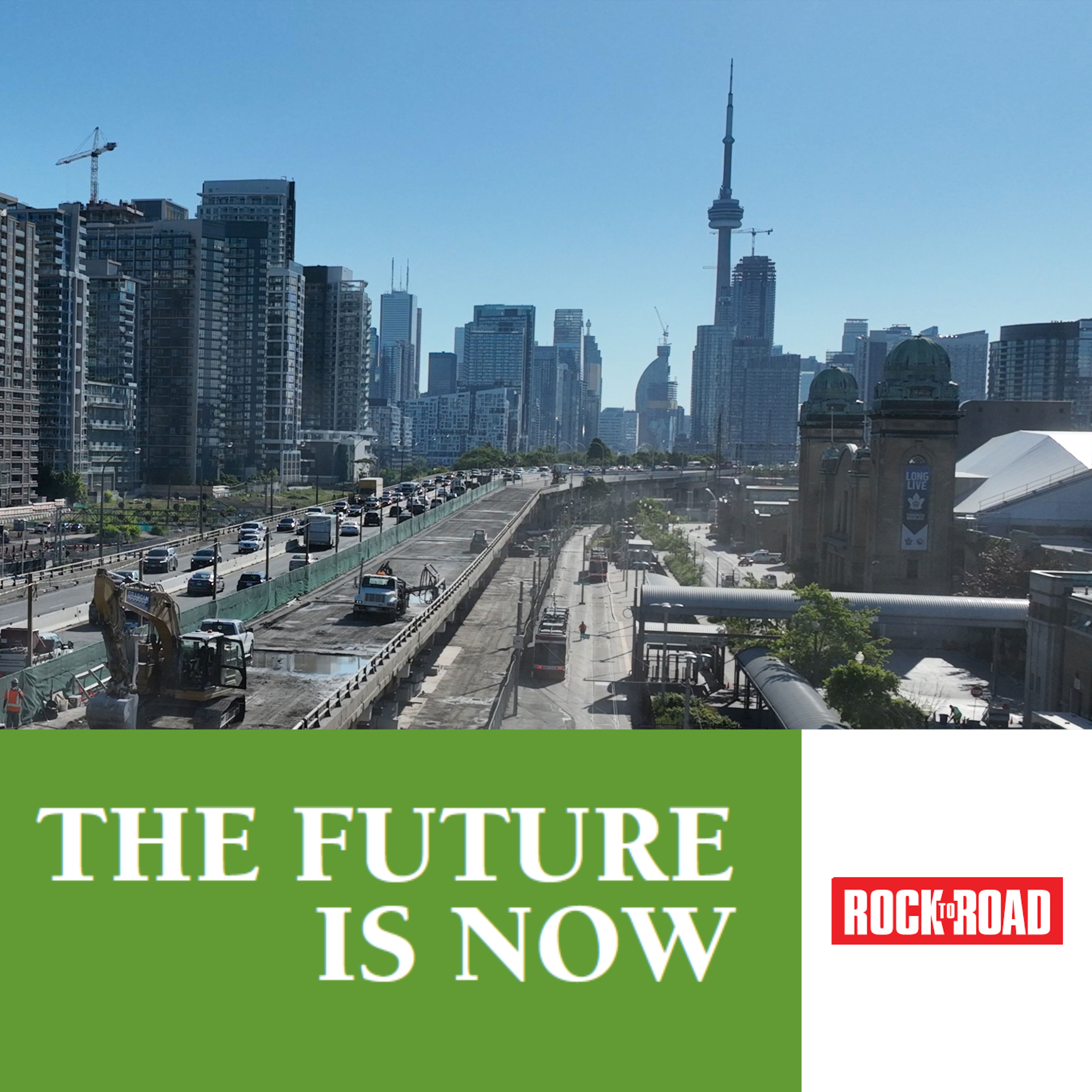
Aggregate Recycling in Ontario FAQS
Yes, both asphalt and concrete are 100% recyclable. These products can be crushed, cleaned and screened, and reused as valuable construction material.
Every year, tens of millions of tonnes of asphalt and concrete are removed from construction sites across Ontario as roads are repaired, bridges are maintained, and other critical infrastructure is replaced. If not recycled and reused, these valuable materials will end up in landfills.
RCM (recycled concrete material) and RAP (recycled asphalt pavement) are processed and reused as aggregate – for example in road bases, shoulders and backfill. RAP can also be reused in making new hot mix asphalt.
A total of about 184 million tonnes of aggregate are used annually in the province. New or primary aggregate (from quarries and pits) meets most of this demand. Only about 13 million tonnes or 7% come from recycled sources.
Ontario’s Ministry of Transportation uses about 20% recycled materials in its 400-series highway construction. According to a report by the province’s Environmental Commissioner, Ontario could avoid extracting up to 33 million tonnes of new aggregate a year if a similar recycling rate could be achieved at the municipal level.
In contrast, some other countries use up to 90% recycled aggregate.
The Ontario Provincial Standard Specifications (jointly administered by the Ontario Ministry of Transportation and the Municipal Engineers Association) sets the standards for road construction and materials in the province. Despite Ontario’s provincial standards, municipalities have discretion in the implementation of these standards and in their local policies. As a result, practices can vary widely by municipality, even in an economically significant region as the Greater Toronto Area, with many choosing to prohibit or severely limit the use of recycled aggregate in road construction and other public works.
This is especially problematic because, collectively, municipalities are the largest consumers of aggregate in the province, using between 60 and 70 million tonnes a year and the largest owner and manager of public infrastructure, more than the provincial and federal government combined.
They may not be familiar with the facts about recycled aggregate or lack experience. As long as the recycled asphalt and concrete conform to OPSS1010, municipalities can be confident that these materials will meet all performance requirements and quality expectations. As responsible owners, they should also do their own quality assurance testing to confirm quality.
If not recycled, these valuable materials end up in our landfills, further exacerbating existing capacity issues, and put further pressure on the operations of pits and quarries to supply primary aggregate. If recycled, but not used, these products end up being stockpiled in growing mountains of urban rubble or, once again, dumped in landfill. Either way, that’s a terrible waste of a precious resource.
By using more recycled aggregate, which is located closer to major construction projects, the need to haul new aggregate from distant pits and quarries is dramatically reduced. This substantially lowers energy consumption and greenhouse gas emissions. It also:
- Keeps aggregates out of the waste stream.
- Reduces pressure to develop and expand pit and quarry operations.
- Results in lower project costs and building more sustainable infrastructure.
Municipalities and other project owners should consider sustainability as part of the initial project design, including in their tenders the ability for contractors to use recycled materials that meets OPSS1010 specifications.
The Ontario Provincial Standard Specifications (jointly administered by the Ontario Ministry of Transportation and the Municipal Engineers Association) set the standards for road construction and materials in the province. OPSS1010 allows aggregate used in road bases, shoulders and backfill to be composed of up to 100% recycled concrete and up to 30% recycled asphalt. Hot mix asphalt can contain up to 30% recycled asphalt pavement.